7 Essential Lubrication Tips to Prevent Machinery Failure
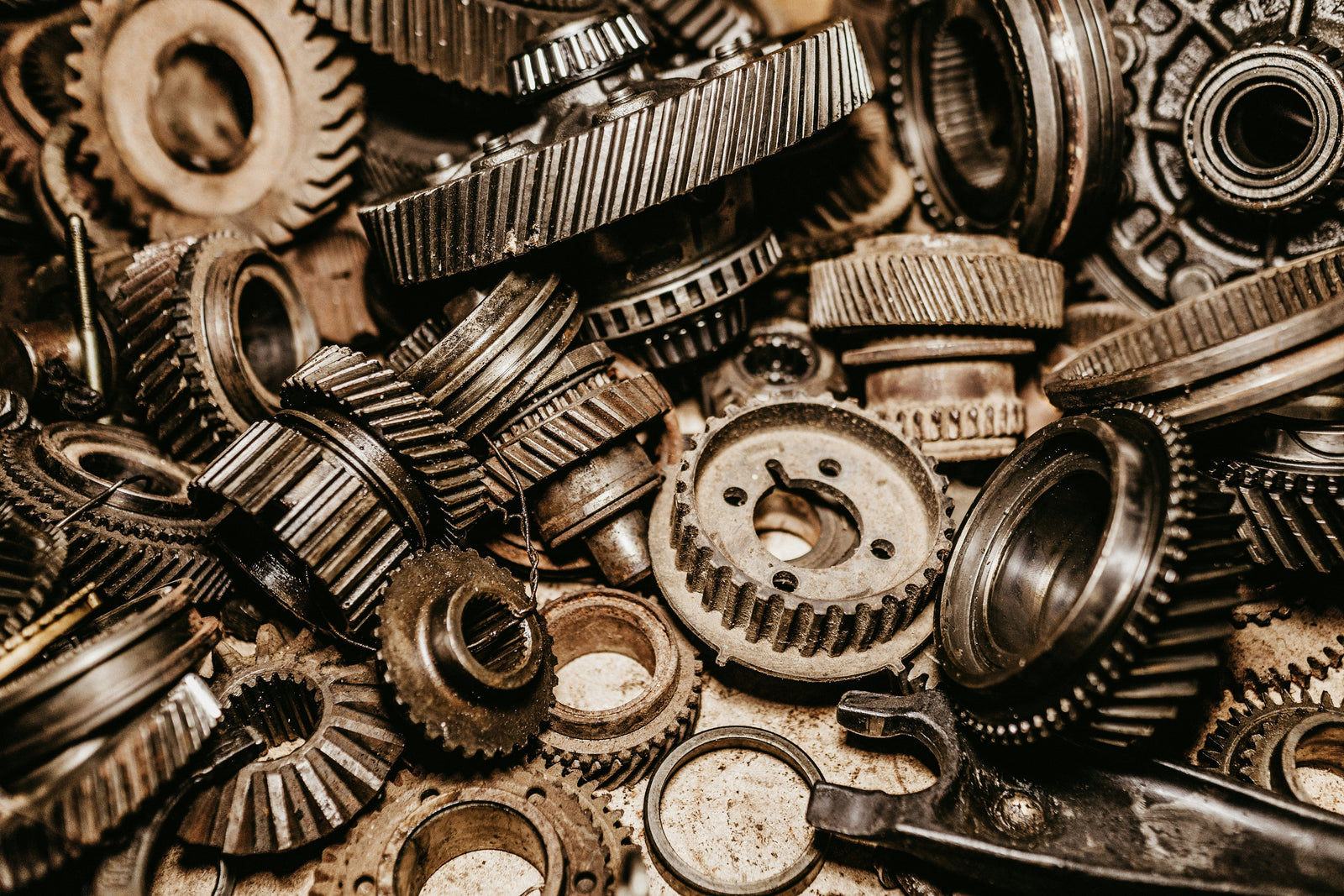
7 Essential Lubrication Tips to Prevent Machinery Failure
Let’s be real—machinery breakdowns are a nightmare. Unexpected failures lead to costly repairs, production delays, and a whole lot of stress. But did you know that over 50% of industrial equipment failures happen due to improper lubrication? (Noria Corporation)
Yep, something as simple as using the right lubricant and applying it correctly can make a huge difference in your equipment’s performance and lifespan. Whether you’re running heavy-duty industrial machines or maintaining smaller equipment, these seven essential lubrication tips will help you avoid breakdowns, cut down on repair costs, and keep everything running smoothly.
1. Choose the Right Lubricant—It’s Not One-Size-Fits-All
Think of lubricants like motor oil for your car—you wouldn’t use just anything, right? The same goes for industrial machines. Using the wrong lubricant can cause overheating, excessive wear, and ultimately, failure.
Here’s what to consider when choosing the right lubricant:
✅ Viscosity Matters: Thicker lubricants work best for heavy loads, while thinner ones are ideal for high-speed equipment.
✅ Temperature Resistance: If your machinery operates in extreme heat, you’ll need a lubricant that won’t break down easily.
✅ Environmental Conditions: Exposure to moisture, dust, or chemicals? You need a lubricant that resists corrosion and contamination.
Pro Tip: Always check the manufacturer’s recommendations before picking a lubricant. TRIPAK’s high-performance industrial lubricants are a solid choice for keeping machinery in top shape.
2. Stick to a Lubrication Schedule
Skipping lubrication is like skipping oil changes for your car—it’s a disaster waiting to happen. Over time, lubricants break down, leading to increased friction, heat buildup, and component wear.
So, how often should you lubricate?
📅 High-speed equipment: Every few days or weekly
📅 Heavy-duty machinery: Bi-weekly or monthly
📅 Low-use machines: Every 3-6 months
If you’re managing multiple machines, set up a lubrication log to track application dates. Even better—consider using automated lubrication systems to ensure precise and timely application.
3. Store and Handle Lubricants Properly
You wouldn’t leave milk out in the sun and expect it to stay fresh, right? The same goes for lubricants. Improper storage can lead to contamination, reducing their effectiveness and putting your equipment at risk.
Best Practices for Lubricant Storage:
✔️ Keep lubricants sealed and stored indoors away from dust and moisture.
✔️ Store them in temperature-controlled environments (ideally 40°F–80°F).
✔️ Use color-coded containers to prevent mix-ups.
✔️ Check expiration dates—yes, lubricants do expire!
According to the Machinery Lubrication Institute, improper storage reduces lubricant effectiveness by 20% (Machinery Lubrication). That’s a big deal!
4. Apply the Right Amount—More Isn’t Always Better
Here’s a common mistake: over-lubricating. Too much grease can trap heat, attract dust, and cause leaks. On the flip side, under-lubricating leads to friction, overheating, and wear.
How to Tell If You’re Doing It Wrong:
🚩 Over-lubrication: Leaking grease, excessive heat, sluggish performance.
🚩 Under-lubrication: Noisy operation, rising temperatures, visible metal wear.
Pro Tip: Automatic lubrication systems can help apply just the right amount, reducing waste by up to 30% (Reliabilityweb).
5. Monitor Lubricant Health—Don’t Just “Set It and Forget It”
Just because you applied lubricant doesn’t mean it’s still doing its job. Over time, contaminants like dirt, water, and metal particles sneak in, reducing its effectiveness.
That’s where oil analysis comes in. Regular oil analysis can detect:
🔍 Metal particles (a sign of internal wear)
🔍 Contaminants (water, dirt, fuel, etc.)
🔍 Viscosity changes (a sign of lubricant breakdown)
Pro Tip: If you’re running heavy-duty machinery, schedule an oil analysis every 6 months. For lighter equipment, once a year should do the trick.
6. Use the Right Lubrication Method
Not all machines need to be greased up the same way. The wrong lubrication method can leave you with ineffective coverage and wasted product.
Common Lubrication Methods:
✔️ Manual Lubrication: Best for small or low-use machinery.
✔️ Automatic Lubrication: Ideal for machines that need frequent lubrication.
✔️ Mist Lubrication: Great for high-speed equipment.
✔️ Bath or Splash Lubrication: Used in enclosed gear systems.
Using the right method improves efficiency and extends lubricant life.
7. Keep Contaminants Out—Your Lubricant’s Worst Enemy
Dirt, dust, and moisture are major threats to lubrication efficiency. Contaminated lubricants lead to sludge buildup, clogged filters, and increased friction.
How to Keep Your Lubricant Clean:
✔️ Store lubricants in sealed containers away from dust and moisture.
✔️ Use high-quality filtration systems to remove contaminants.
✔️ Regularly inspect machinery for leaks and dirt buildup.
According to the National Lubricating Grease Institute (NLGI), contaminated lubricants cause 75% of premature bearing failures (NLGI).
Final Thoughts—A Small Investment in Lubrication Saves Big in the Long Run
At the end of the day, proper lubrication is the easiest way to prevent machinery failure. It keeps your equipment running smoothly, reduces maintenance costs, and prevents unexpected downtime.
Quick Recap:
✅ Use the right lubricant for your machinery.
✅ Stick to a regular lubrication schedule.
✅ Store lubricants properly to prevent contamination.
✅ Apply just the right amount of lubricant.
✅ Monitor oil health with regular analysis.
✅ Use the correct lubrication method.
✅ Keep lubricants clean and free from contaminants.
If you want to extend the life of your equipment and save thousands on repairs, invest in high-quality lubricants like TRIPAK’s industrial solutions.
Your machines (and your wallet) will thank you.